31.08.2011 | Insight
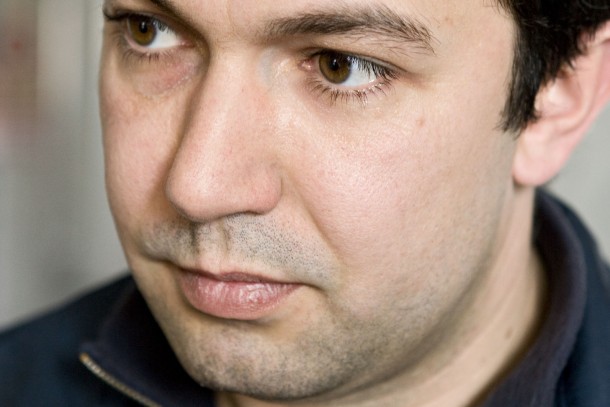
Fresh bread and margarine are not one of the first things that come to mind on a visit to the OJSC Kiev Margarine Factory located not far from the city centre of Ukraine’s capital.
The production process has been automated to the extent that the golden mass bubbles under the surface in silver-coloured pipes and cisterns completely out of sight until we enter the packaging department. Here an army of women in white are standing along the conveyor making sure that the blocks of the end product are neatly wrapped in aluminium foil and then placed in cartons ready to be delivered to shops and restaurants across the country.
The OJSC Kiev Margarine Factory accounts for about 30 per cent of the domestic output of margarine in Ukraine. The company also makes cooking oil and mayonnaise. One of its best known brands is Olkom, a name that adorns the margarine packets in shops. Even in the throes of a recession and financial crisis, demand for this type of basic commodity remains relatively steady generating a solid cash flow for the company. Last year, the company’s turnover reached EUR 38.3 million.
Recently, the OJSC Kiev Margarine Factory was modernised by replacing the existing heat exchangers, installing new low-energy pumps and upgrading the sequential control system. Most of the technical equipment for the project was supplied by Alfa Laval of Sweden.
“It was Alfa Laval that recommended NEFCO when we were exploring the options for applying for a loan to finance the project,” says Chief Engineer Alexandr Kravchenko.
NEFCO extended a loan of EUR 350,000 for the project from its Revolving Facility for Cleaner Production. Repayments are based on the savings to be generated by the project. The Fund is authorised to finance up to 90 per cent of the total investment costs of similar projects that help save energy and reduce emissions harmful to the environment. In this case, the project contributed to lower emissions of mainly carbon dioxide, sulphur oxides and nitrogen oxides.
“Thanks to the upgrade to the production process and reduced power consumption we’re able to save over EUR 79,000 per year. As an additional bonus, we’ve been able to improve production efficiency to the extent that today we produce 100 to 120 tonnes more margarine than before,” explains Kravchenko.
The company also recovers production residue, for example by selling fat to local soap makers. In doing so, they follow the same regime as applied by many factories in the West. But the Finnish and Ukrainian margarine cultures diverge on at least one point. My questions about the local debate on cholesterol levels and the effect they have on the company’s product development efforts raise a laugh.
“We don’t really have that sort of debate here in Ukraine – I can’t remember any customer ever asking for a low-cholesterol or cholesterol-reducing margarine,” concludes Kravchenko with a wide grin.